This project was built independently for mechanical Prototyping as an exercise in prototyping complex moving mechanical systems.
Given the prompt of building an automata, I immediately thought about the philosophy of creating mechanical life that inspired clock makers to produce fantastically complicated devices that walked, talked, and even ate. Hands are an expressive and complex body part that I thought would be quite fun to model using linkages, a type of mechanism we had previously learned to design.
Checkout the animated 3D model:
Project goals:
- Produce a mechanism from a CAD model using a laser cutter and basic shop tools
- Explore a variety of mechanisms like linkages and cams
- Use SolidWorks to create animations
- Use clock cage as main structural component
Design Constraints:
- Materials limited to 1 sheet of 1/8th" hardboard, dowels, fasteners, and 3d printed parts
- No hot glue or tape!
Timeline:
- 1 week for design and modeling, 1 week for fabrication and assembly
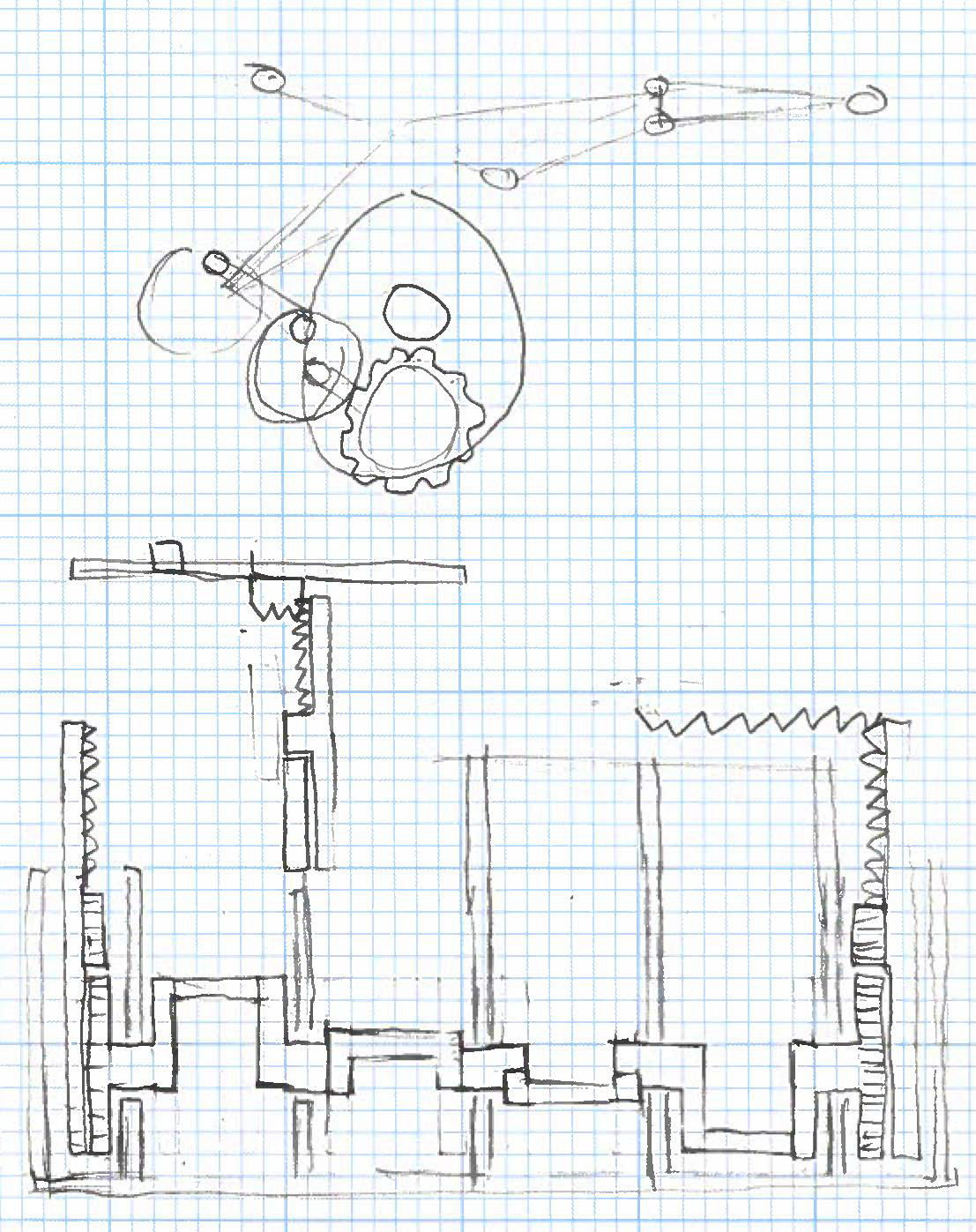
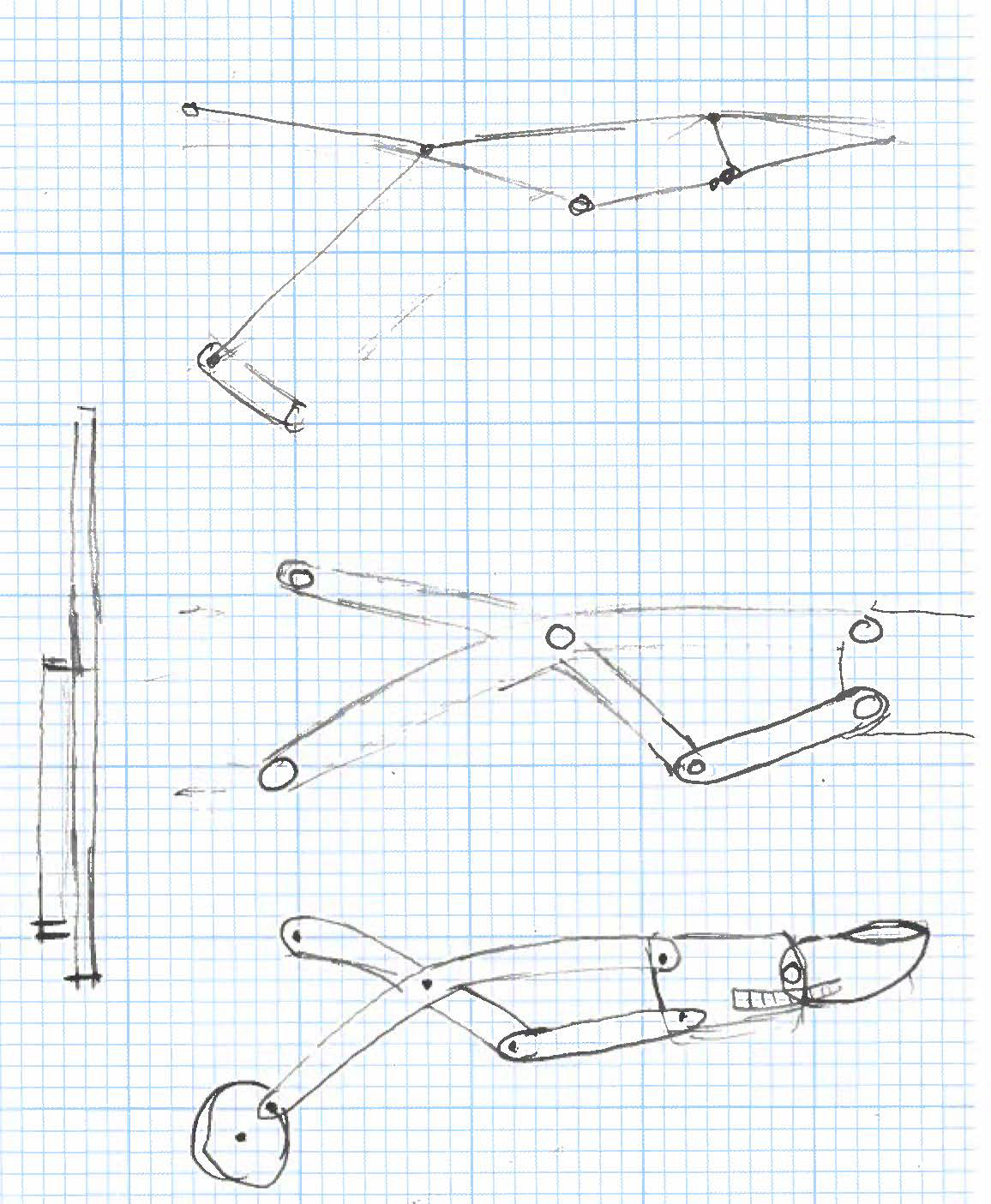
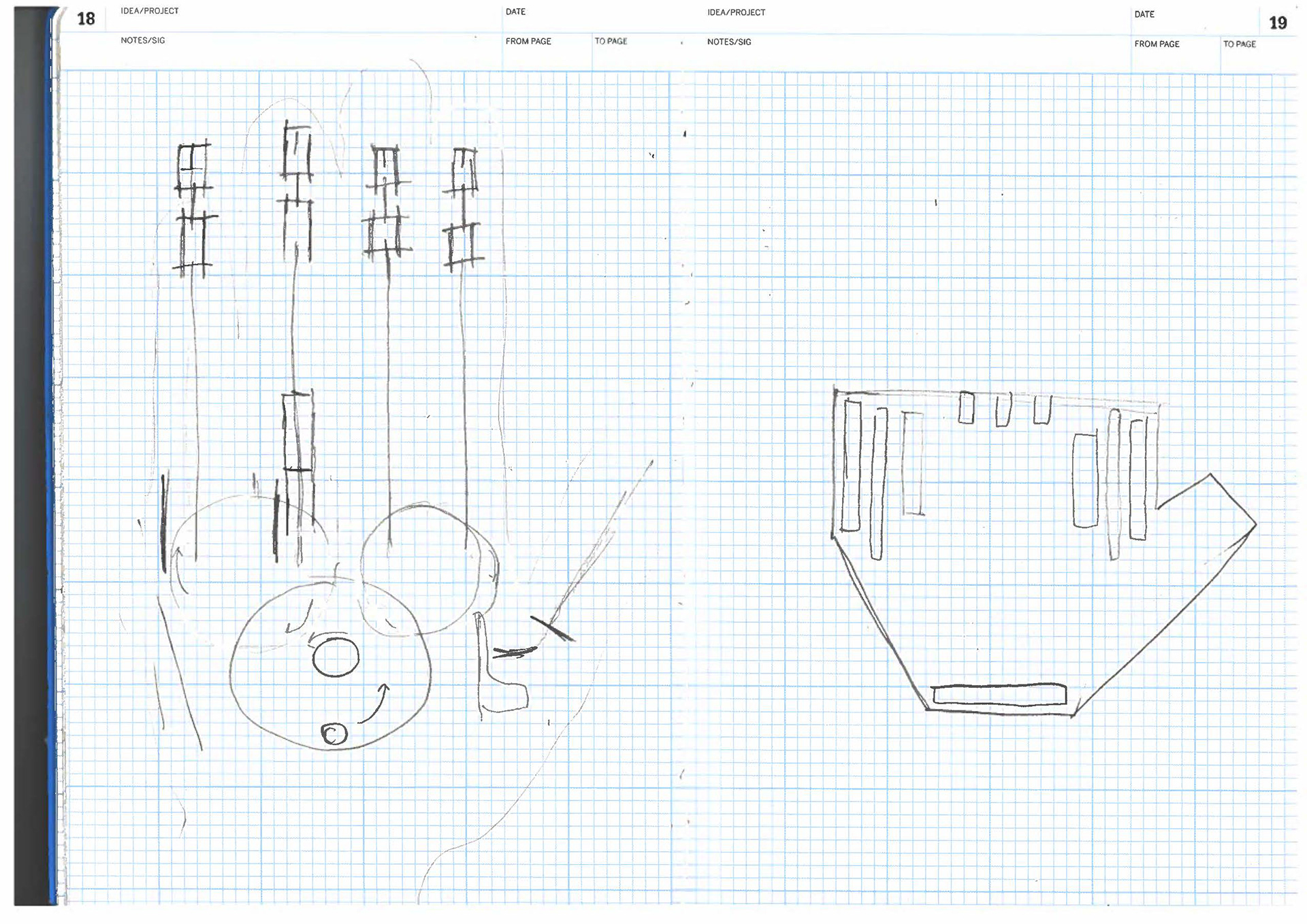
every project starts with a sketch
I came up with a gear reduction drive train, a crankshaft to cyclically offset the finger motion, and a rough geometry for the linkages.
I used a specialized linkage design software to further refine the link lengths to get a motion that accurately resembled reference of idly tapping fingers
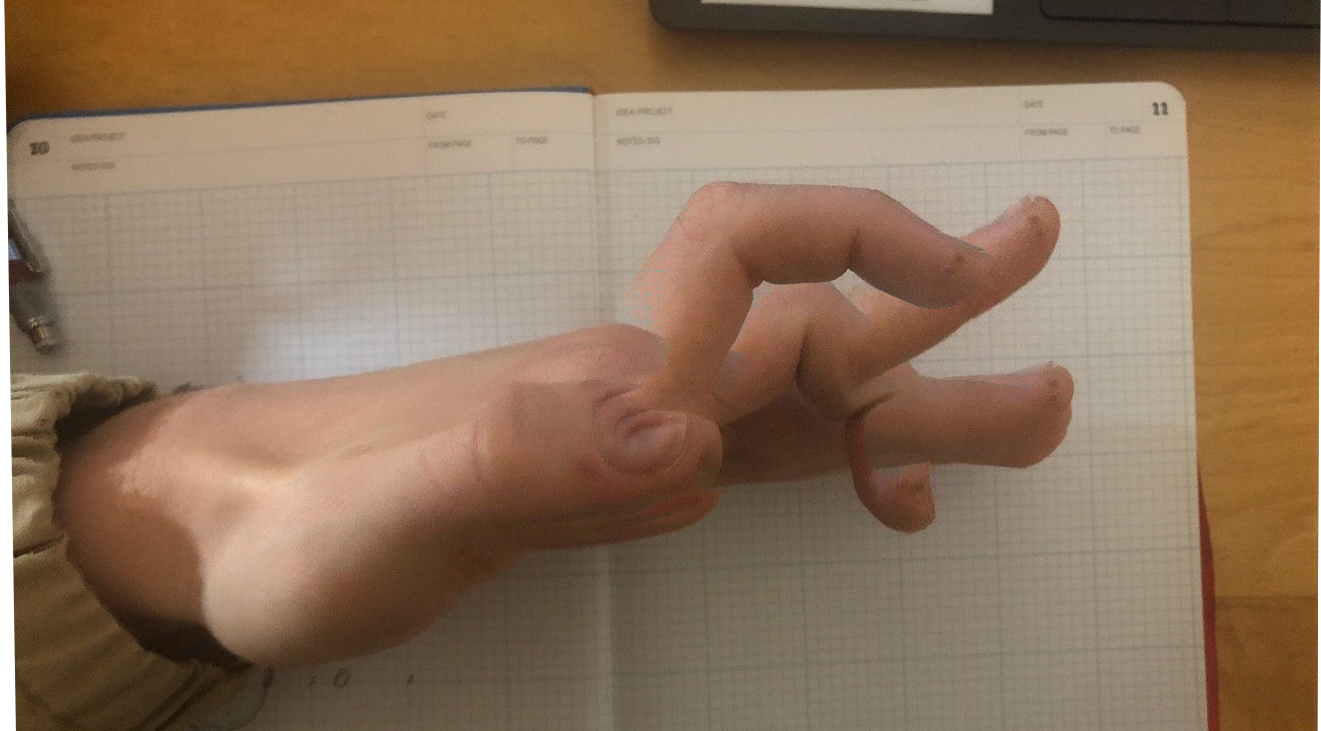
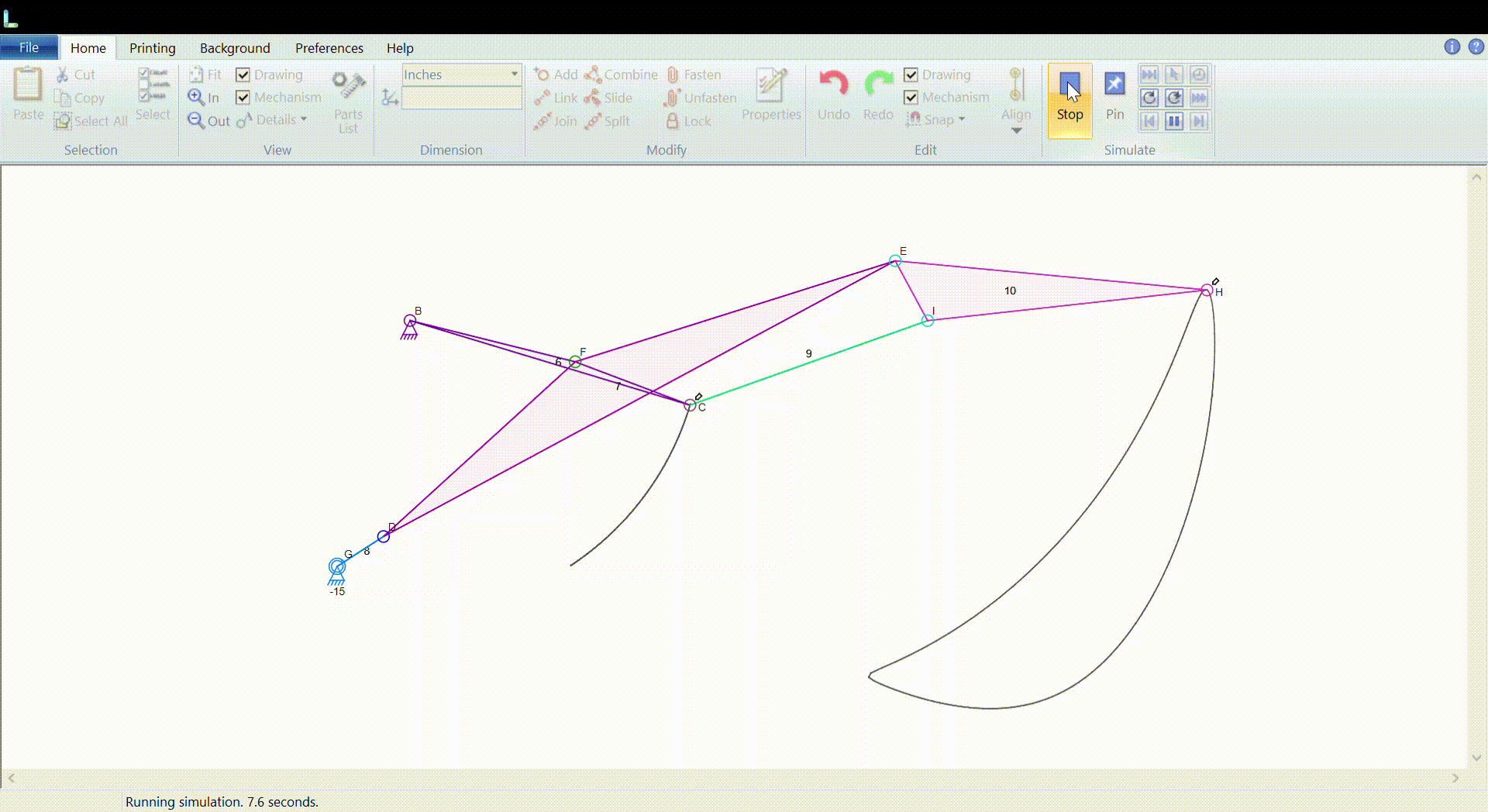
I brought the linkage dimensions into SolidWorks, and developed a full 3D assembly with functional mates to simulate the final motion and check for any interference or collision. the final design
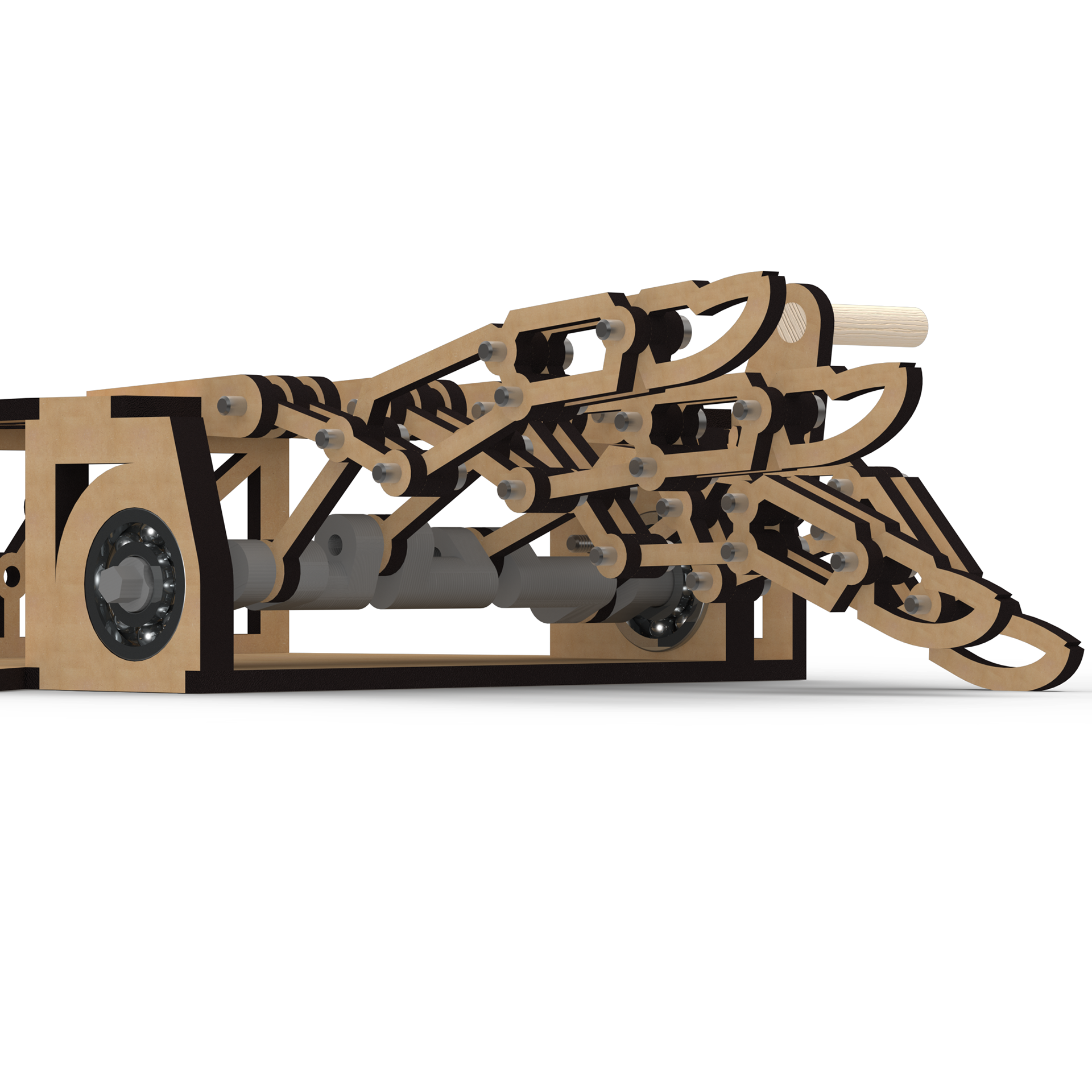
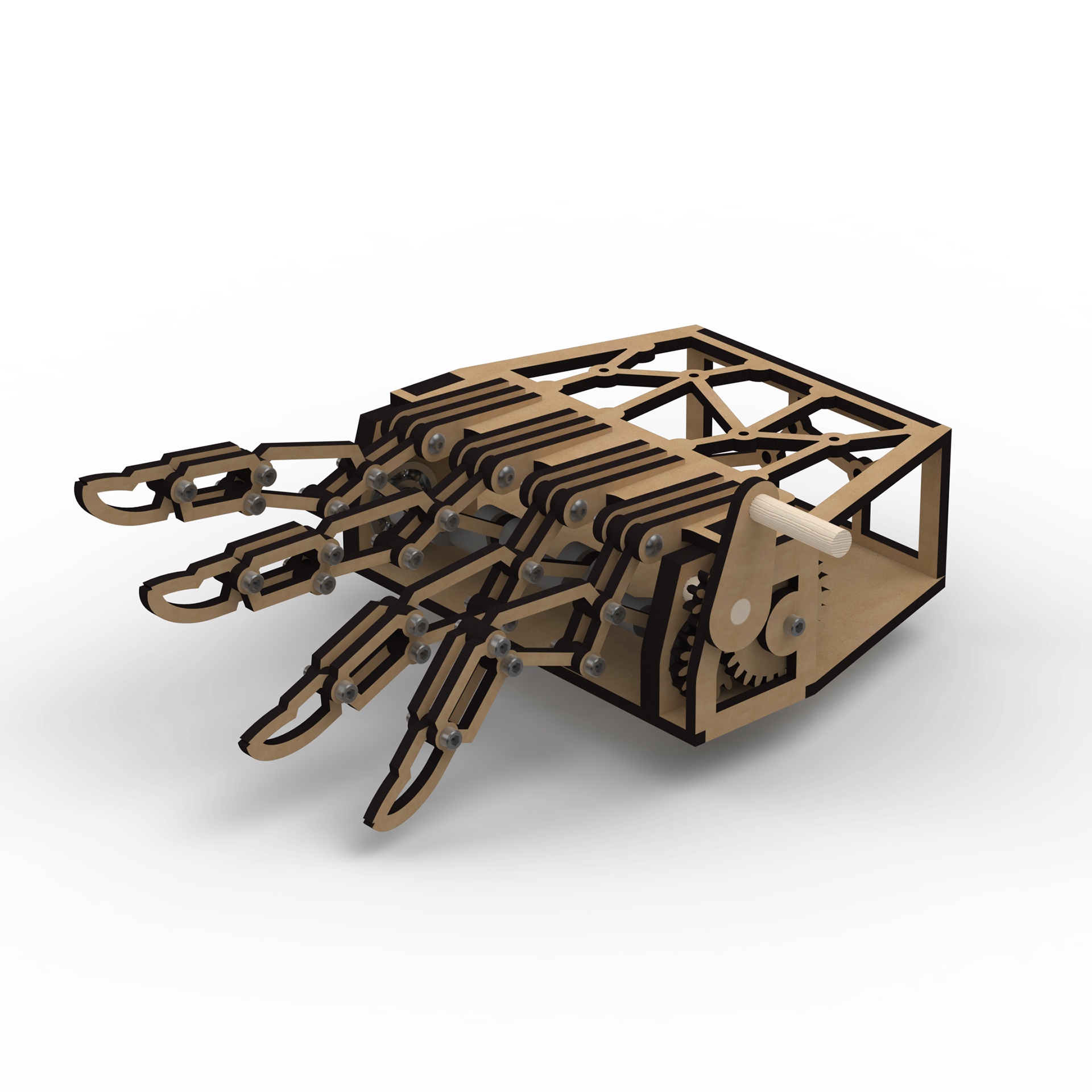
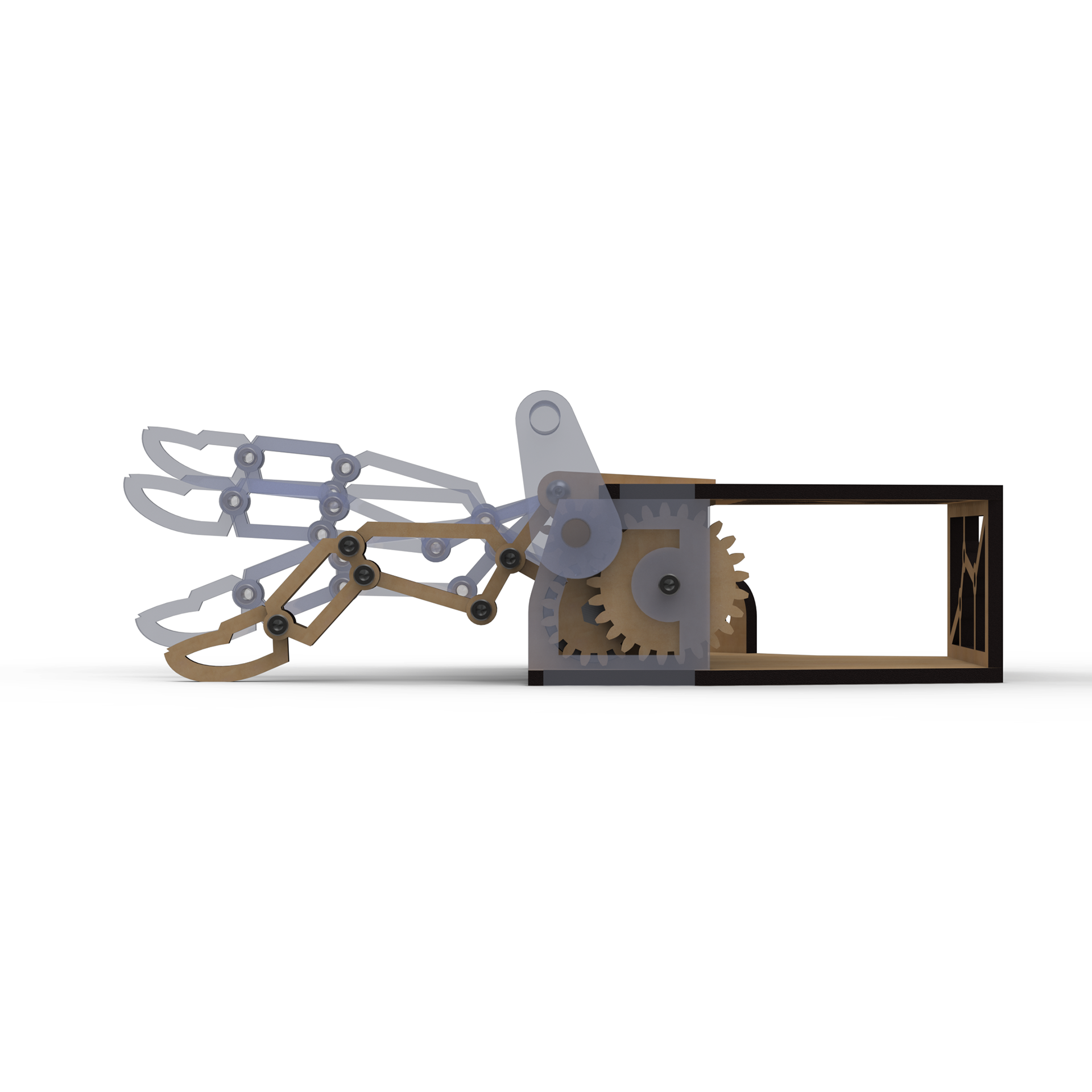
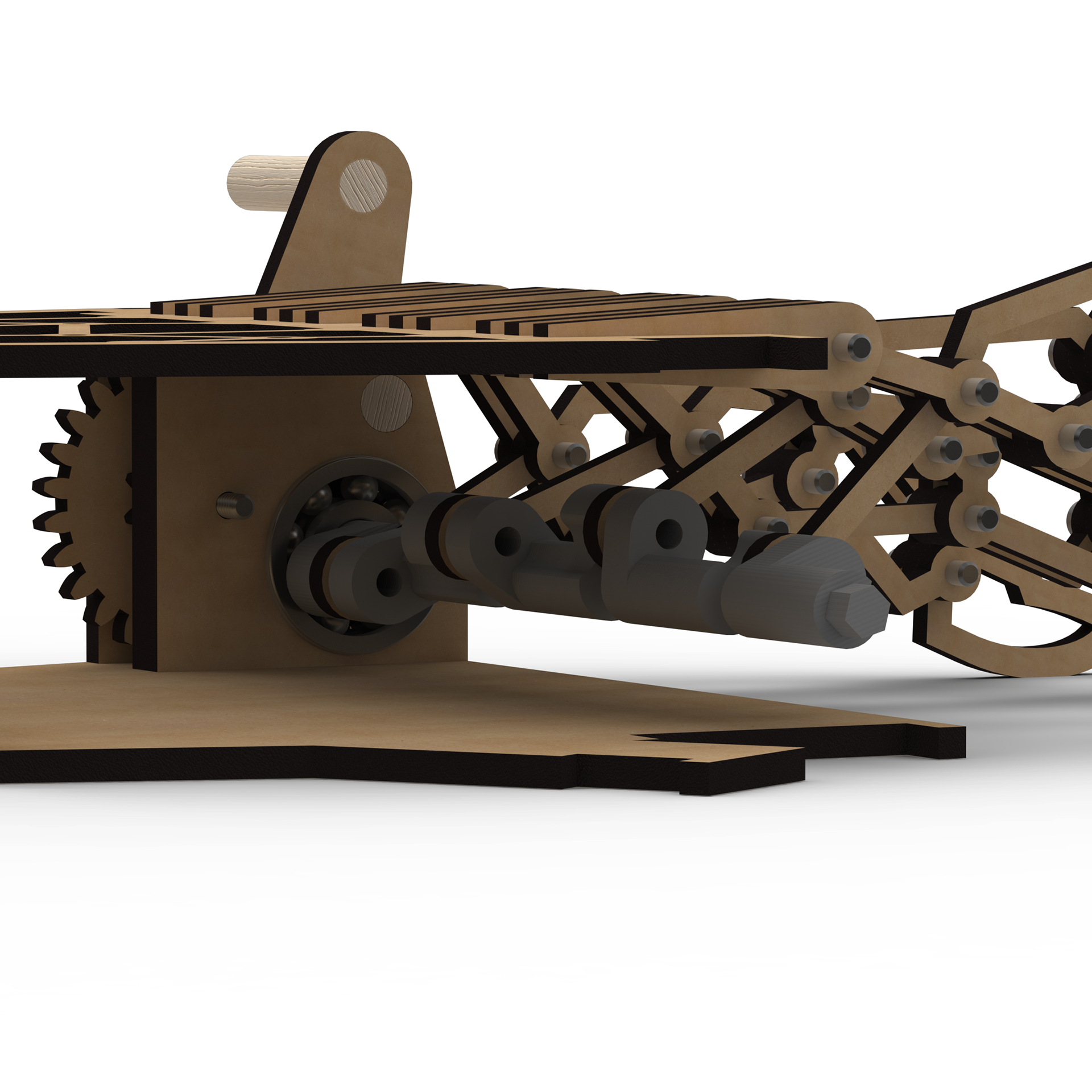
I laser cut and 3d printed all custom components, and carefully glued and fastened the assembly, finding some spare bearings from career fair fidget spinners. The final product had a very satisfyingly smooth action, and a perfectly uncanny motion.
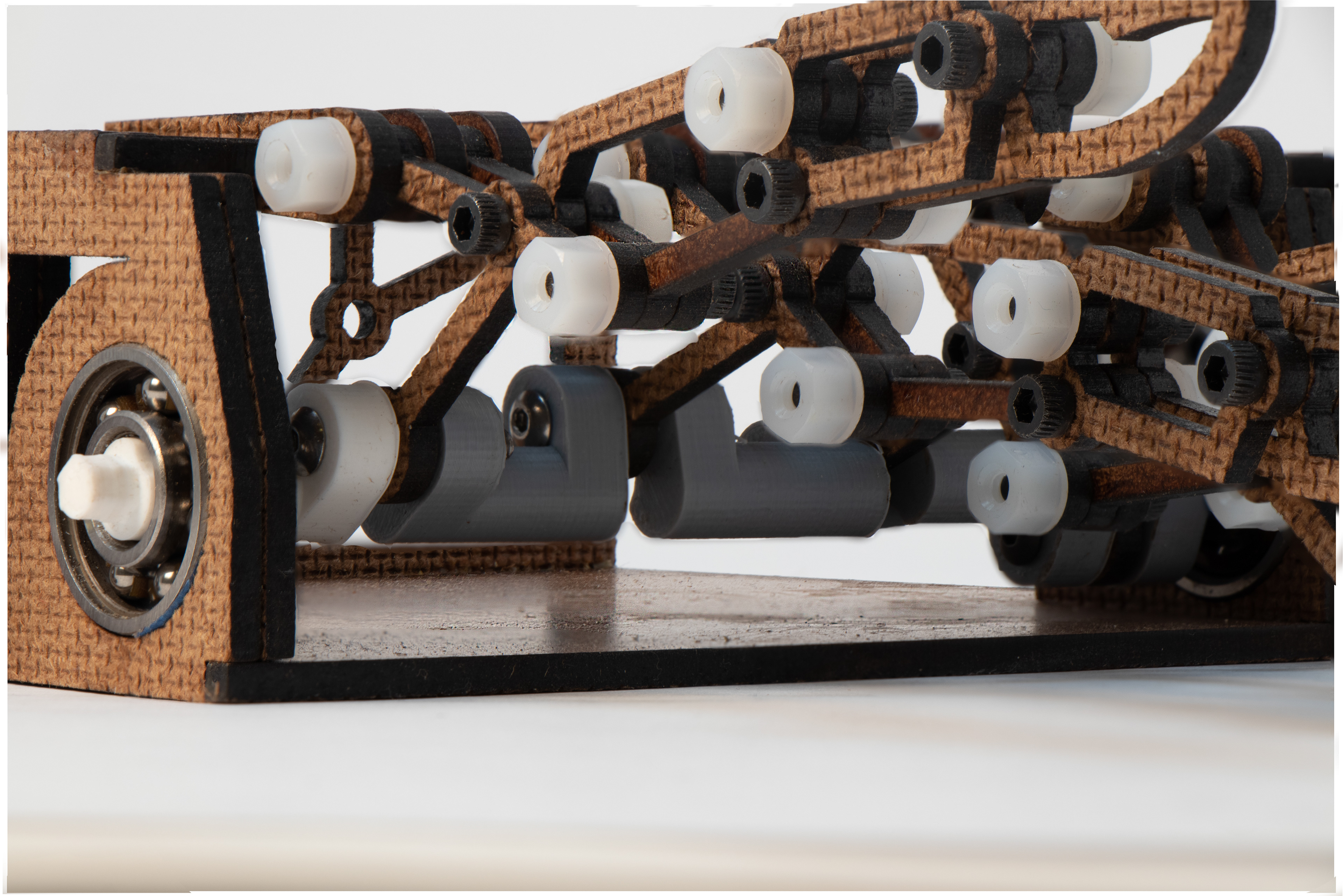

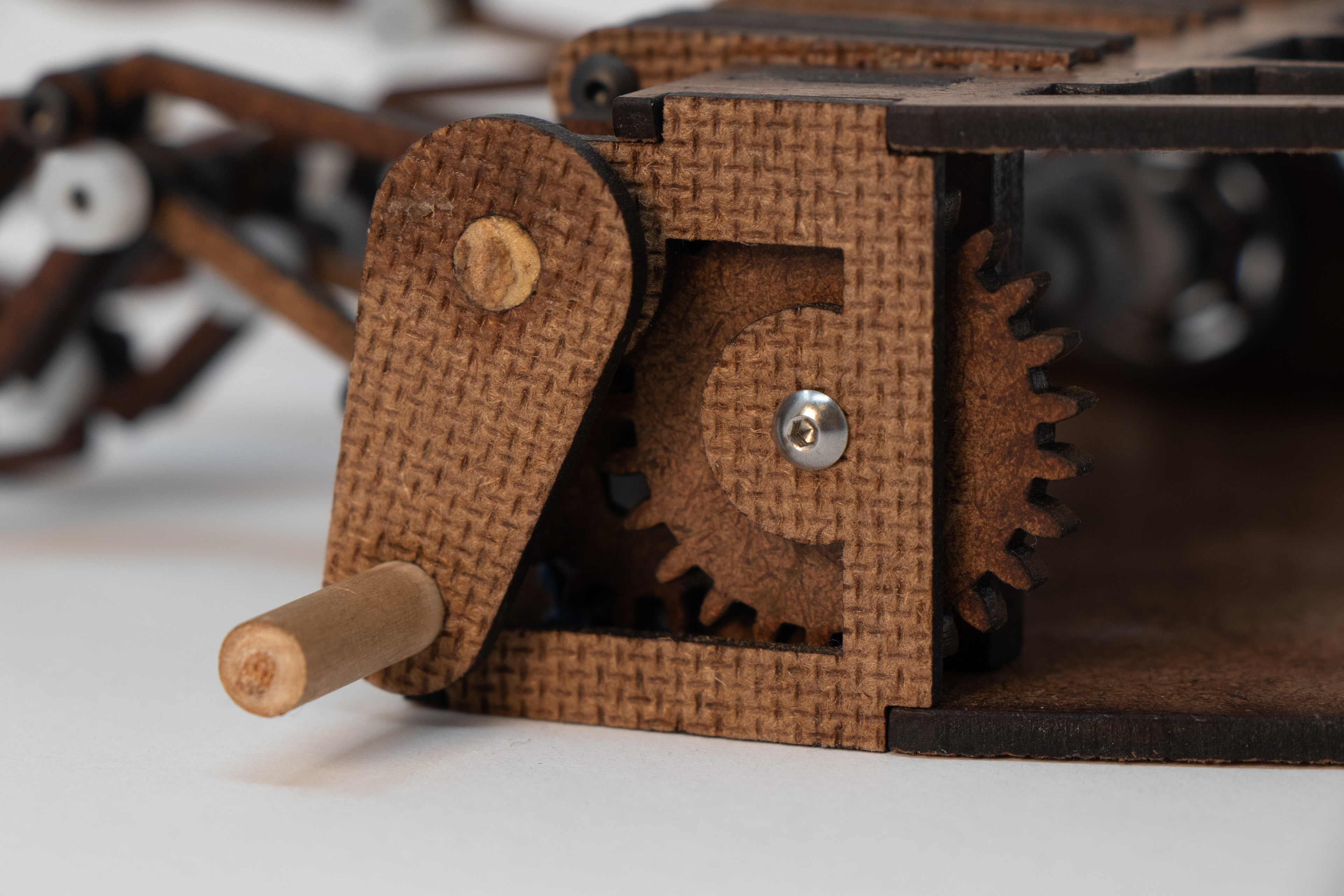
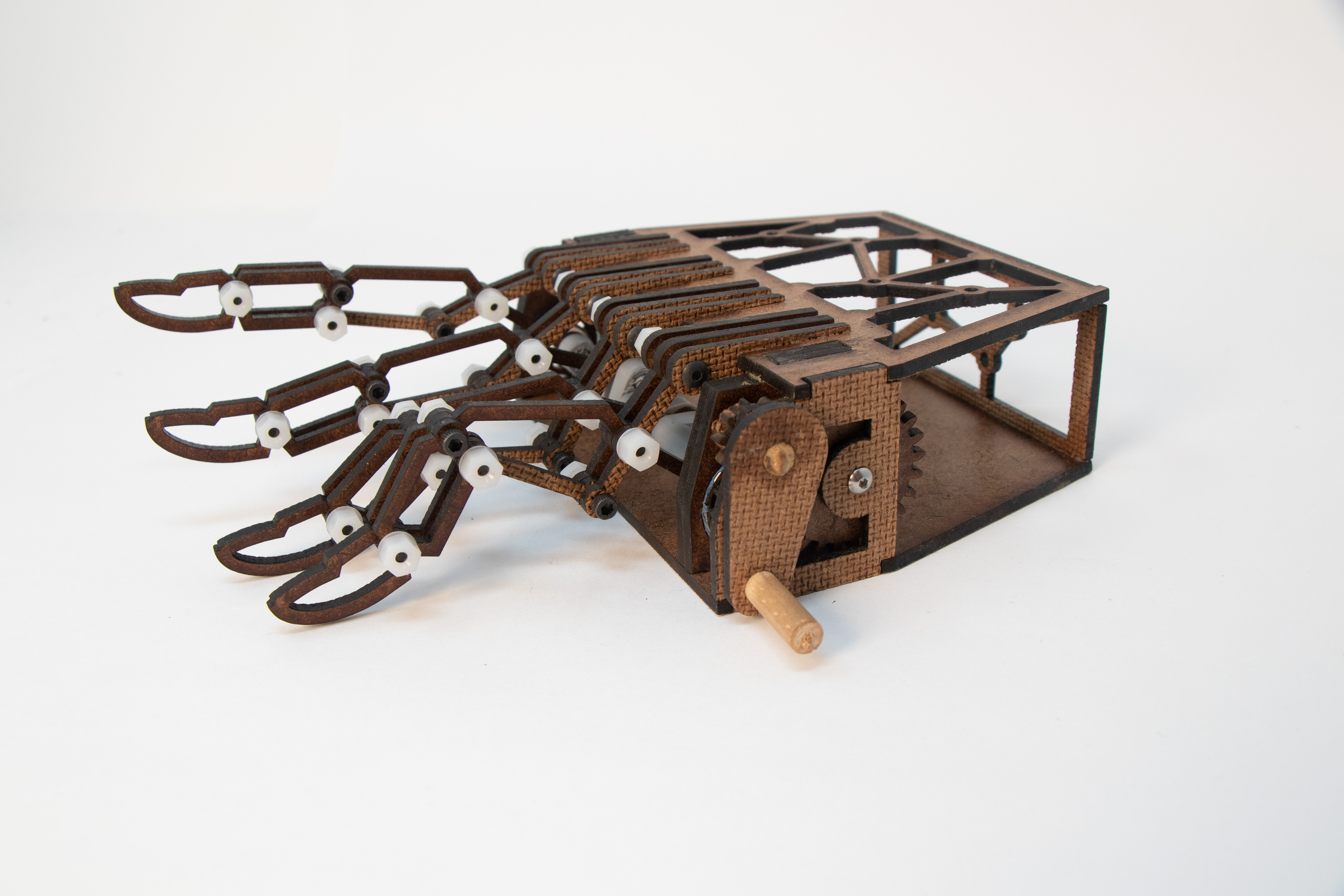
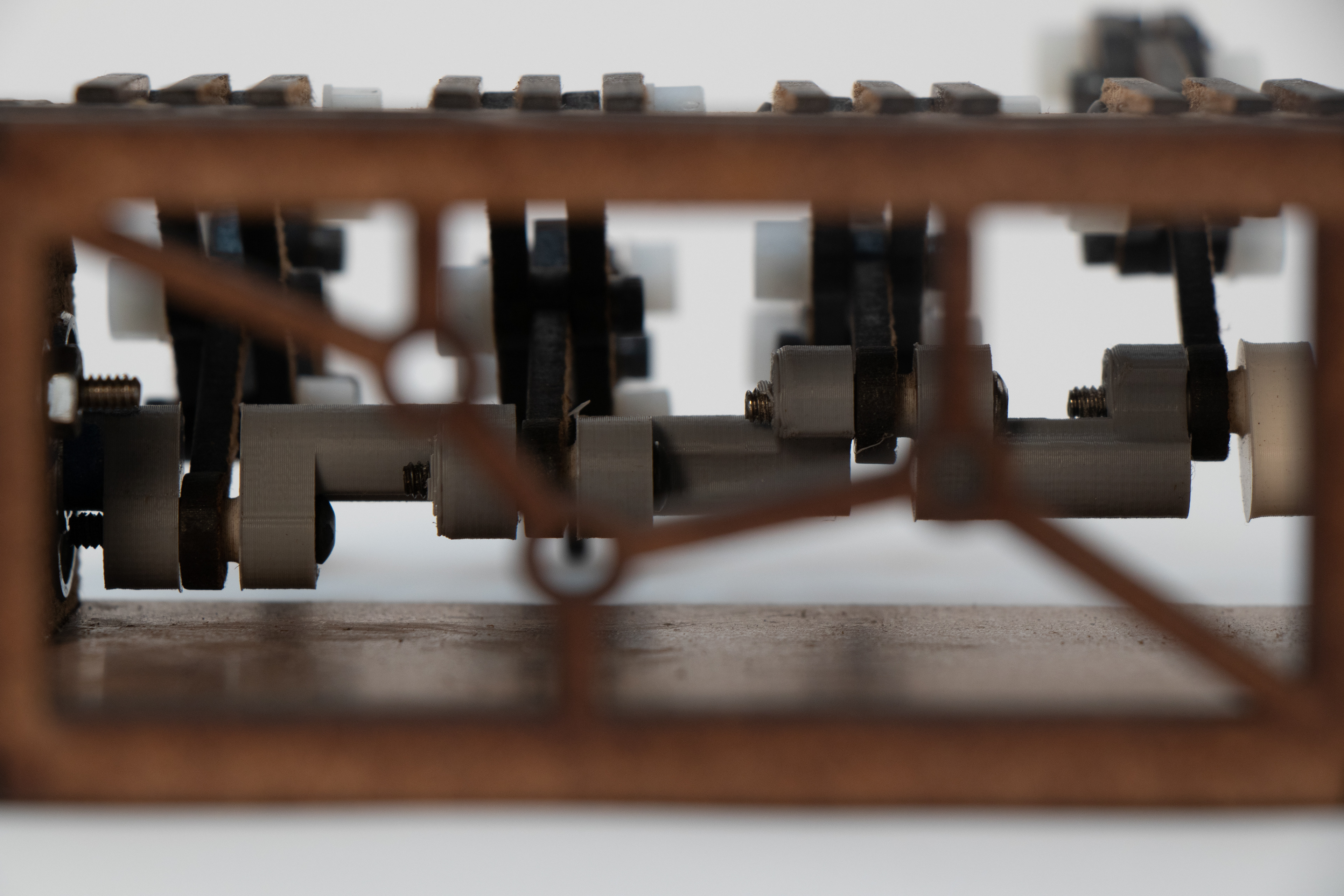
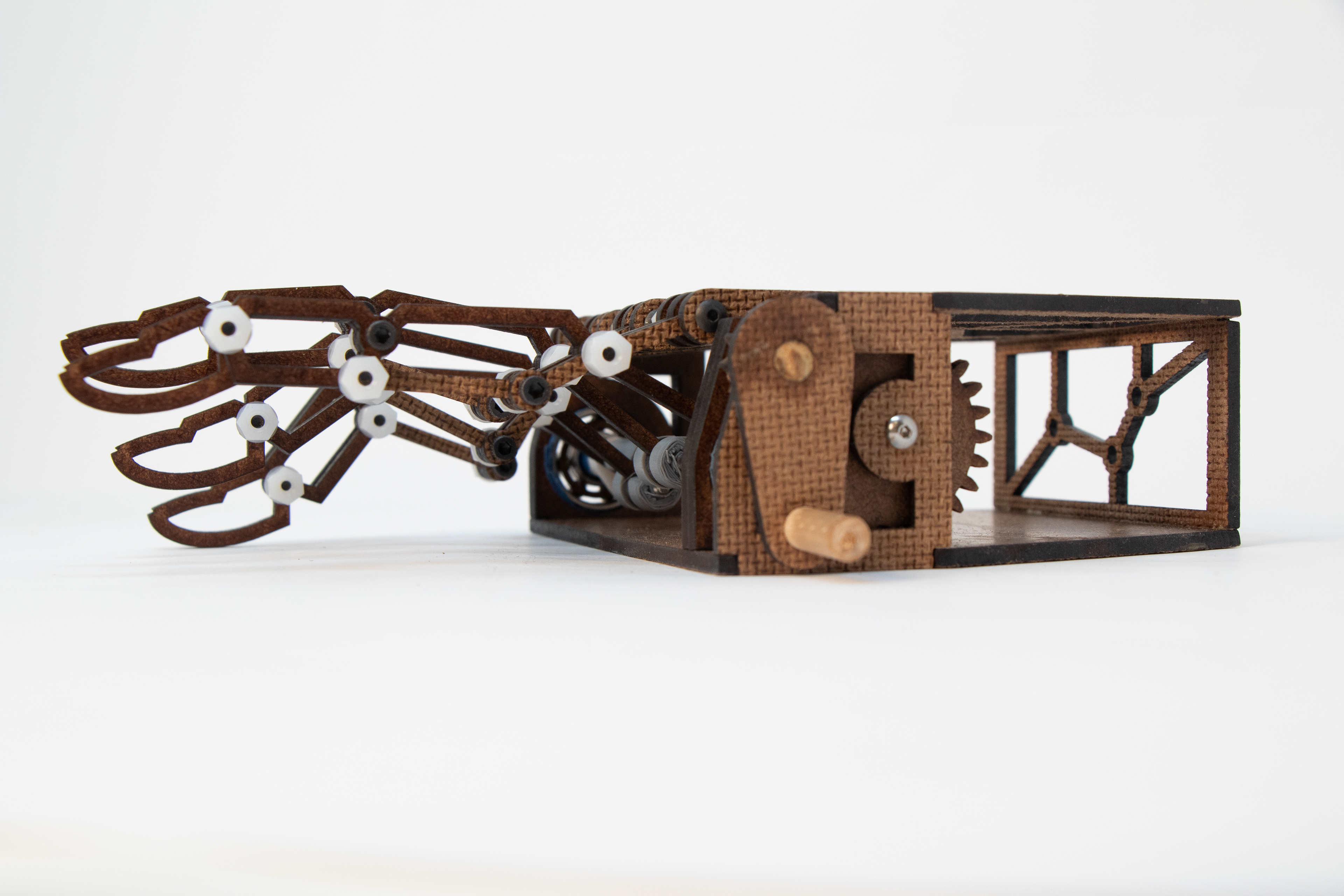
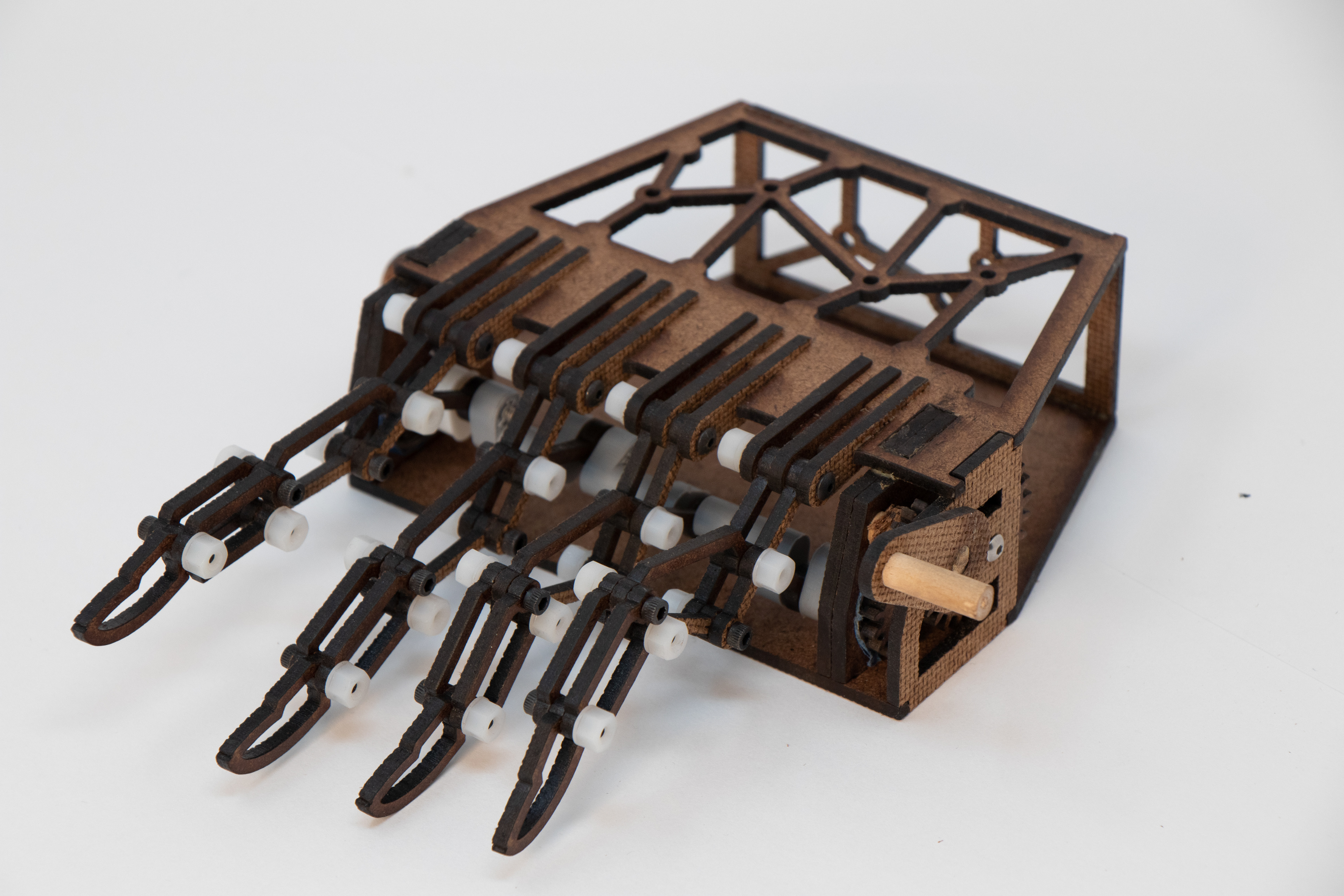
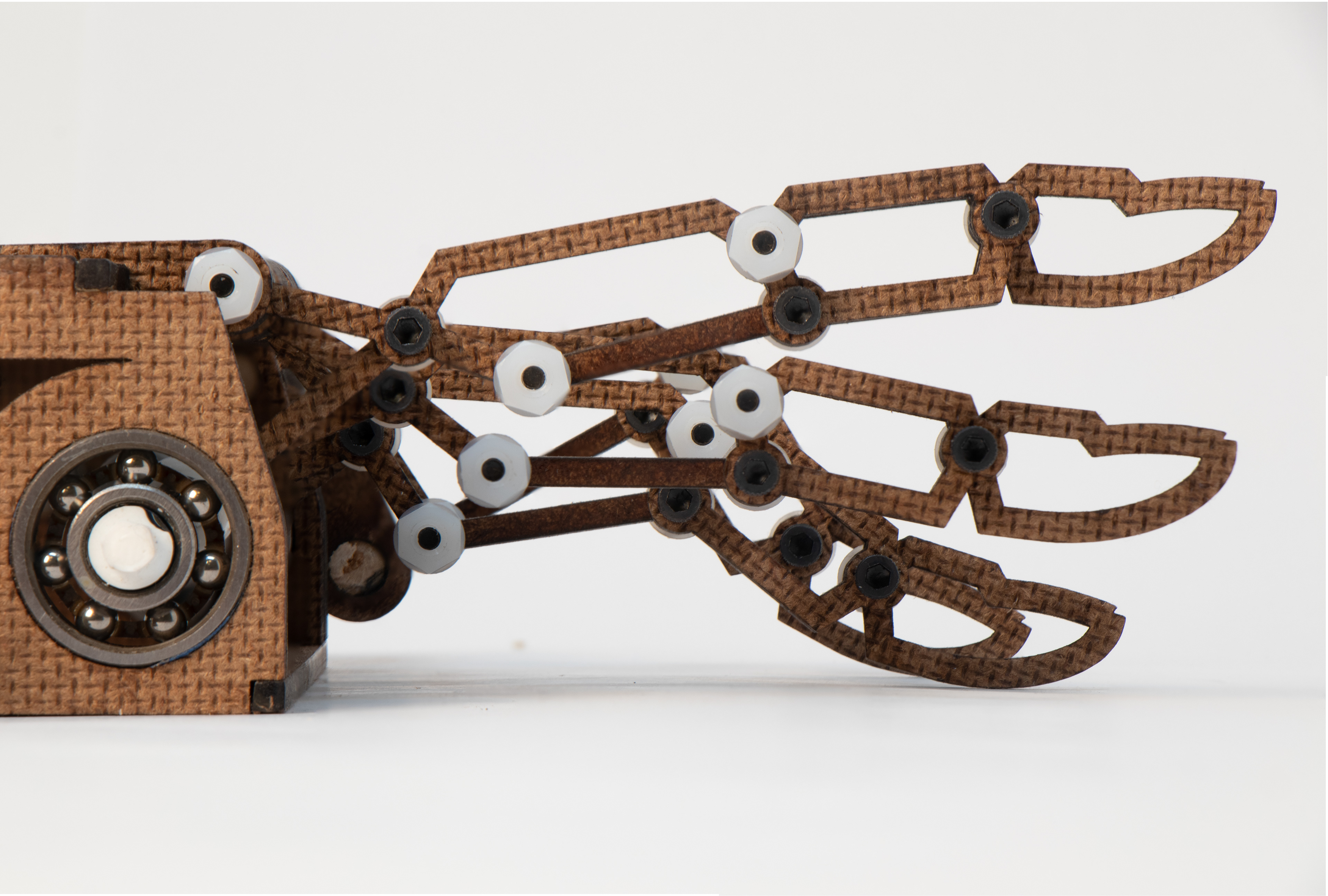
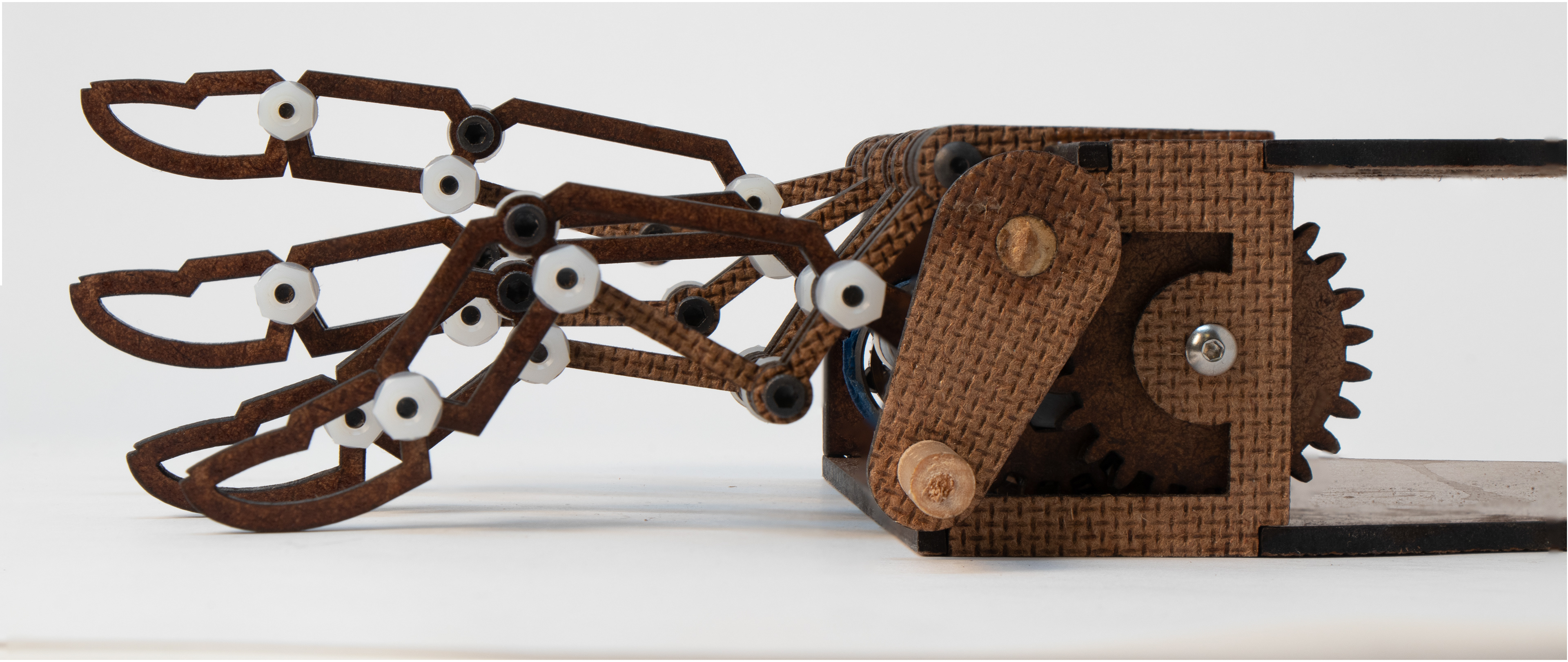
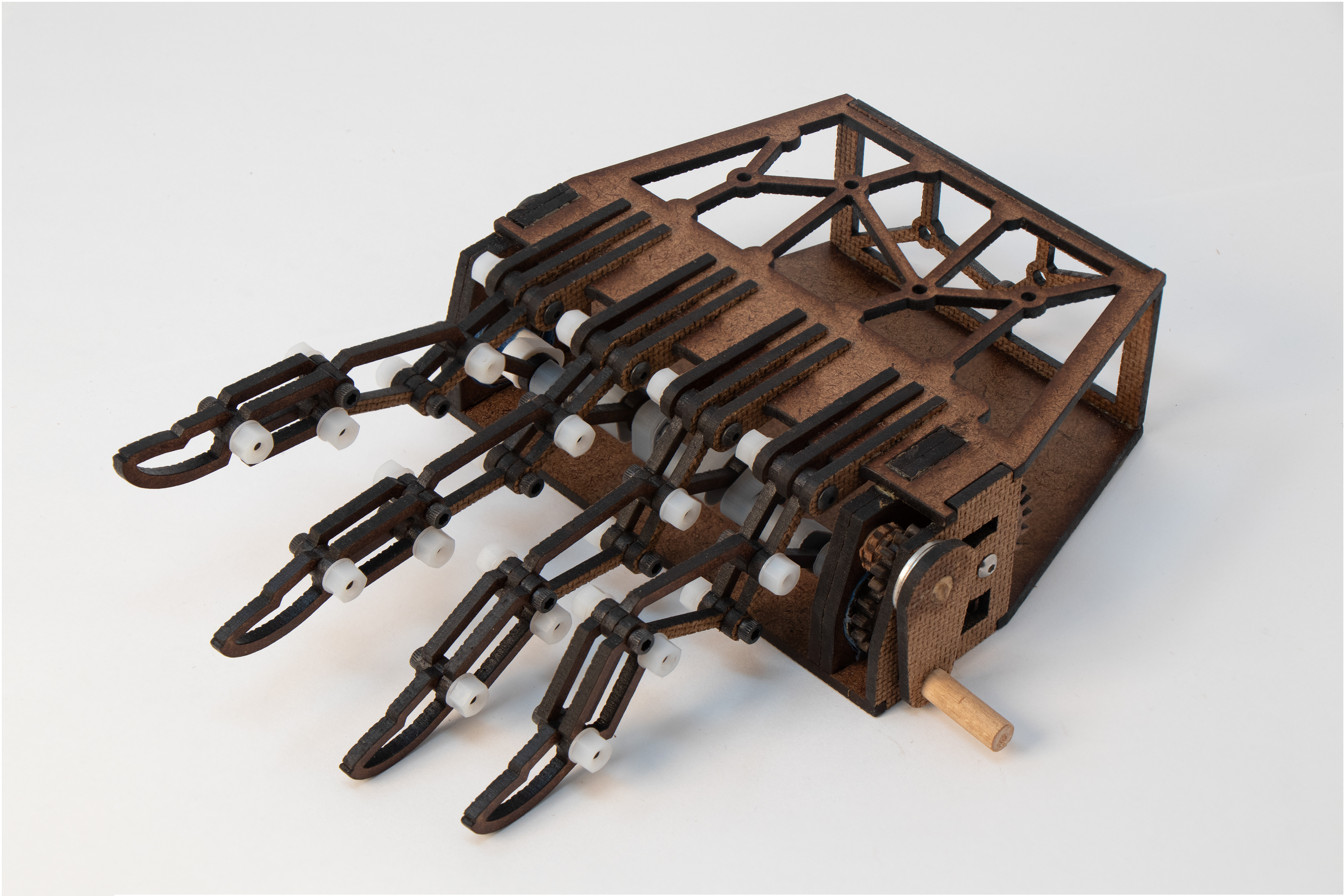